BGA Board Assembly
Electronics items such as laptops and cell phones have become increasingly popular in the modern information age due to the rapid expansion of the electronics industry. People have begun to place ever-increasing demands on electronics devices in terms of features and performance, while placing ever-increasing demands on volume and weight. Multiple functionality, light weight, and miniaturisation have been the primary development trends in modern electronics items up to this point. To reach this goal, IC (integrated circuit) chip feature sizes must be reduced while their complexity level continues to rise. As a result, the number of I/O ports increases, as does the I/O density of the package. To meet the development requirements, some innovative high-density packing technologies have emerged, of which BGA (ball grid array) is a key type since it offers more competent advantages in terms of light weight, compactness, and high performance than other packaging types.
BGA Board Assembly packaging was first introduced in the early 1990s and has since evolved into a mature high-density packaging technology. BGA packaging technology has been widely used in PC chips, microprocessors, ASICs, arrays, memory, DSPs, PDAs, and PLDs, among other applications.
BGA Assembly Procedures
- BGA SMT is closely associated with solder paste, components, PCB, silkscreen and soldering among which soldering items are the most difficult to be dealt with in reflow soldering process.
- Reflow temperature curve consists of four phases: preheating phase, heat preservation phase, reflow phase and cooling phase.
- Heating process and temperature curve should make package reach reflow temperature and then fall back to that of pad after solder balls are melted with inter-metallic compound generated with pad.
Pre-BGA Assembly
- Prebaking: BGA usually absorbs humidity. If a chip is instantly heated after absorbing humidity in the air, moisture diffusion will lead to cavities inside chip. Hence, general baking condition of BGA packages are done under 120°C for 24hours/ according to MSL level in TDS.
- Oxidation Inspection: Prior to their applications, BGA components are inspected to ensure their pins are clean and go through none oxidation.
- Solder Paste Printing Inspection: Inspecting the solder paste printing of BGA pads will helps to eliminate the soldering defects occurring after soldering. Check for the height, shape, bridge/short, overflow, missing/skip are done visually to ensure better quality & connectivity after re-flow.
BGA Assembly
- In-line X-ray Inspection:
BGA chips are be mounted at last after placing all the other components onto the PCB using SMT pick & place machine, and then subject to an in-line x-ray inspection for verifying the alignment of BGA pads to the PCB’s. This helps to find out & eliminate the misalignment & solder short issues. - Re-flow Soldering:
The BGA chips are soldered using the ref-flow oven (16 zones) with the help of pre-set thermal profiles. The thermal profiles are programmed considering several factors of the BGA from it’s TDS. The best suited re-flow profile will ensure a high quality solderability.
Post-BGA Assembly
- Visual Inspection (2 stage-QC check):
The reflowed PCBA are allowed to cool for 30-40 sec as touch free time. The solderability check(shorts/bridging, voids, misalignment, shift, cross, less solder, excess solder) are done by passing the controllable high intense light beam in-between the BGA solder balls. These visual are verified/recorded using 300x magnifier & the monitor . Pinching the sideway solder balls are performed to ensure the soldering strength too (non-destructive test). - Cold Test / Impedance Test:
Checking the impedance across all the related capacitors connected through the BGA power rails are done to find out short/open circuits. - X-ray Inspection:
Taking X-ray of the BGA chips will allow to filter out any sort of soldering related issues. These are done to pinpoint the exact issue before performing any re-work or repair on the non-working boards. - BGA rework :
Rework & Reballing are done with the aid of automatic BGA re-work station, in which the thermal profile for de-soldering, soldering & re-balling are pre-programmed. This ensure boards quality even after any critical re-work.
Sample Products with BGA's assembled
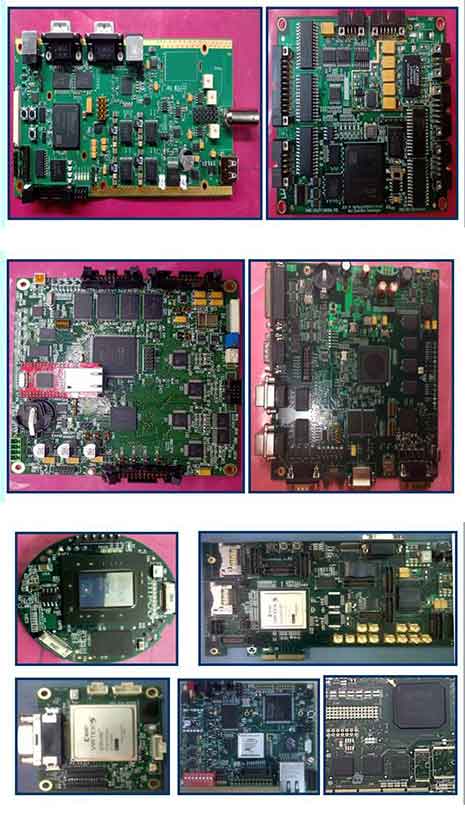
EMSxchange Enables you to select a Printed Circuit Board assembly suppliers meeting your Required PCBA Manufacturing Capability, capacity and Certification Criteria from a global PCB Assembly manufacturer base. EMSXchange takes complete responsibility and ownership for your electronic manufacturing process and all its deliverables from contract manufacturing supplier selection to manufacturing to quality inspection to shipment and delivery to your door. EMSxchange Electronic Manufacturing Partners Profile includes:
Argus Sytems (AESPL) – PCBA, Cable Assembly, Box Build.
Cerra Systems inc – PCB Manufacturing.