Long Term Storage
Where single or multiple productions are planned within a single procurement then the ability to store parts over a long period must be considered. Long Term Storage is not placing the parts on a shelf and forgetting them for years. Customers who have taken such risks have suffered greatly from the poor reliability of the parts to the increased costs of additional procurements and the effects of obsolescence on their design stability and future production schedules.
If significant procurements are planned, then long term Storage must be viewed as being like taking out insurance. If the insurance option is not taken up, then there is a greater risk of loss of the investment and the high probability of significant additional costs associated with investigation, replacements, alternatives, re-design, re-qualification and delayed production.
It is therefore very important to specify and control the long term Storage process.
Long Term Storage Risks
The threat to the stored parts is obvious but many other factors will result in either a risk to the part or a real threat to the continued use of the part.
The main threats can be summarised as follows:
- Obsolescence
- Handling and ESD
- Traceability and Stock Control
- Alerts NCR’s and Failure Analysis
- Change notices
- Inspection and Test
- Packaging
- Part consumption, spares etc
- Store environment
- Store monitoring, Audit
- Procurement Documentation
- Datasheet & Specification
- Provider,security,insurance
- Relife
Degradation or deterioration during stock holding will vary from little or none to severe, according to a number of parameters which include:
Part Related
- Component technology
- Component package
- Lead material
- Packaging and intermediate packaging
- Extent of handling prior to storage
- Cleanliness of part
- ESD
Storage Related
- Temperature stability
- Humidity stability
- Duration
- Handling
- ESD
- ‘Dry’ sealed packaging
- Special considerations, magnetics etc.
Effects of poor Long Term Storage controls
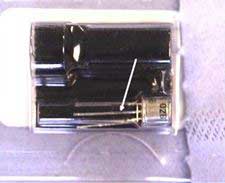
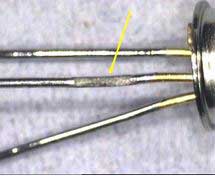
Lead (Pb) in the leadout finish has been oxidised by the antistatic finish on the shipping package
Examples of poorly solder finished leadouts exposing pure tin near the microcircuit package
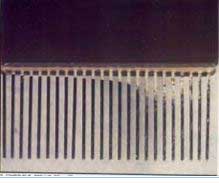
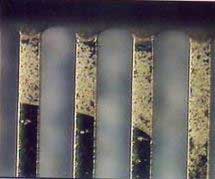
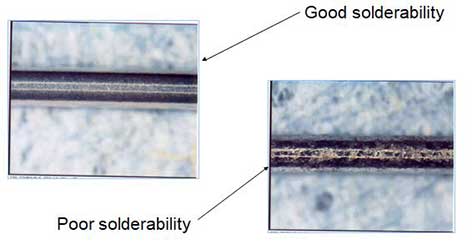
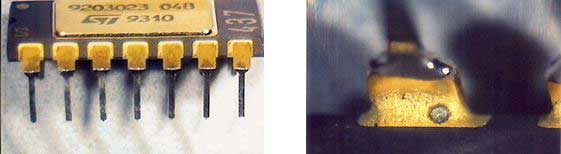
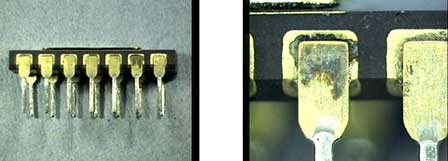
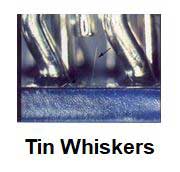
EMSxchange uses a unique, proprietary vendor evaluation & qualification system to onboard vendors. We maintain a close view of their capability, capacity, and compliances. 25+ years of manufacturing experience has given us strong capabilities to understand customer requirements and supplier capabilities. EMSXchange takes complete responsibility and ownership for your electronic manufacturing process and all its deliverables from contract manufacturing supplier selection to manufacturing to quality inspection to shipment and delivery to your door. EMSxchange Electronic Manufacturing Partners Profile includes:
Argus Sytems (AESPL) – PCBA, Cable Assembly, Box Build.
Cerra Systems inc – PCB Manufacturing.